
Machine Safety Services, Risk Assessments & Mitigation Planning
Cybertrol understands that functional safety is not a one-size-fits-all approach. Every plant has unique needs, and ensuring the safety of personnel and equipment requires a collaborative effort between OEMs, system integrators, and plant operations teams. From machine operators to operations managers, our team is equipped to work with your entire organization to implement safety solutions that align with industry standards and best practices.
Plantwide Functional Safety Services
Functional safety is a critical aspect of industrial operations, safeguarding both employees and equipment from hazardous conditions. With evolving regulations and the increasing complexity of automation, ensuring compliance and mitigating risk have never been more important. Our approach to functional safety is designed to integrate seamlessly with your existing control and information systems, providing a comprehensive solution that enhances workplace safety, maintains regulatory compliance, and improves overall operational efficiency.
At Cybertrol, we don’t just implement safety solutions—we develop customized strategies to address the unique challenges of your plant. Our team includes certified functional safety engineers (TÜV Rheinland) with expertise spanning the entire safety lifecycle: from initial risk assessment and system design to implementation, validation, and ongoing support. Whether you need to safeguard individual machines, assess plantwide risks, or develop long-term functional safety plans, our certified engineers have the knowledge and experience to help you achieve your safety and operational goals.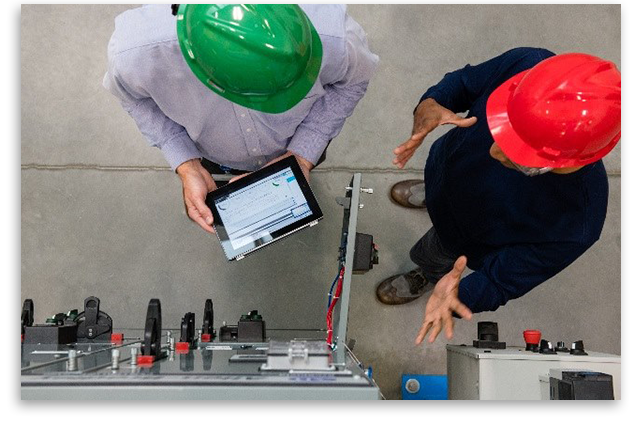
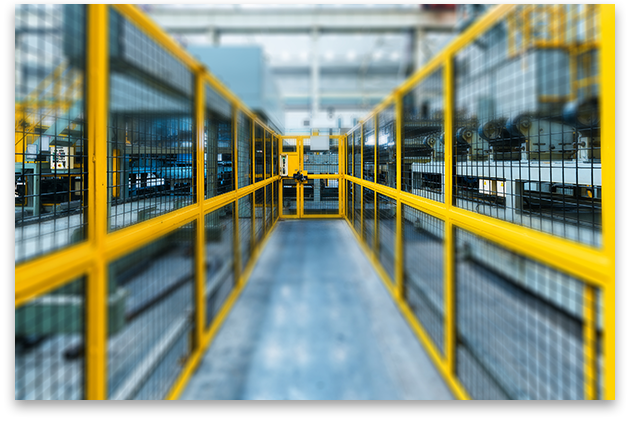
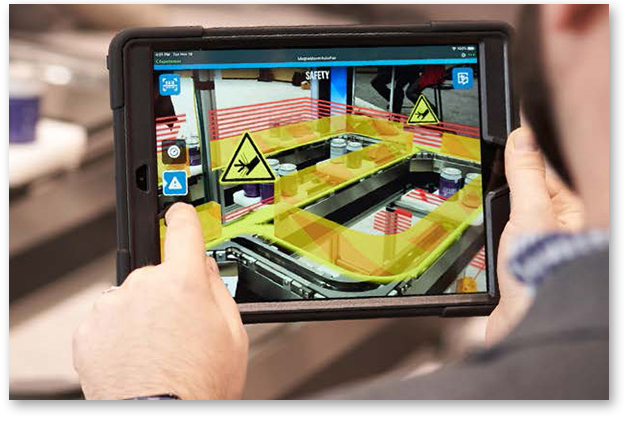
Machine Safeguarding
Ensuring the safety of your machinery is necessary for maintaining a safe and efficient work environment. Our machine safeguarding services help you comply with industry regulations and reduce the risk of incidents by implementing effective safety controls. We provide:
- Risk assessment and safety requirement specification documentation
- Safety-related controls and programming
- SISTEMA reports for safety function design and validation
- System verification and validation to ensure compliance and functionality
- Continuous maintenance and modifications to safety system
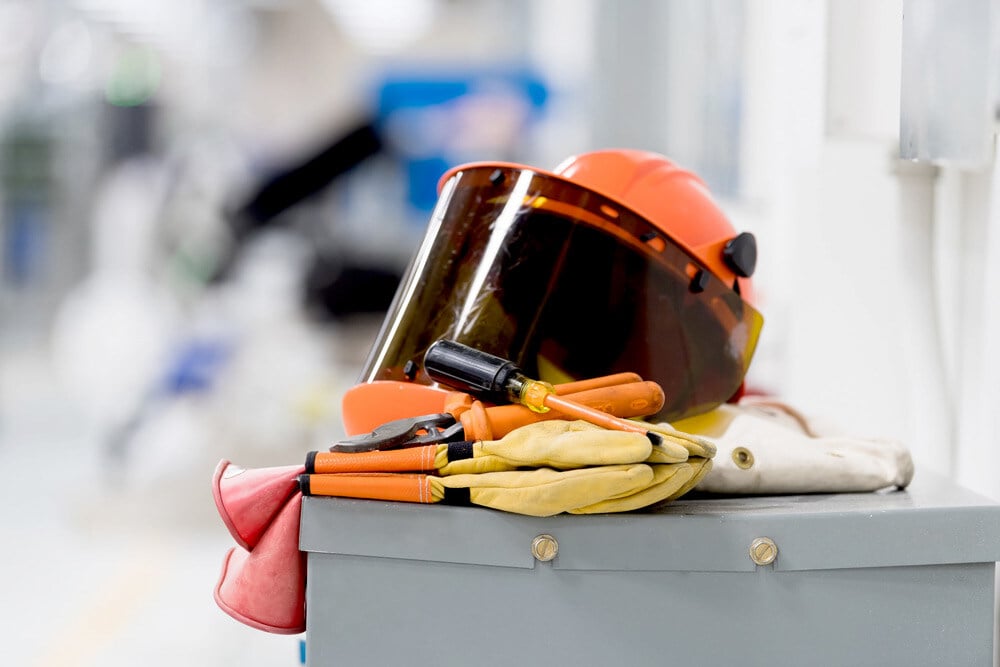
Comprehensive Safety Solutions
Functional safety extends beyond individual machines—it requires a plantwide approach. We offer holistic solutions to assess, identify, and mitigate risks across your facility. Our services include:- Plantwide risk audits to evaluate safety gaps
- Individual risk assessments tailored to specific machinery or processes
- Team-based task risk assessments to engage operators in the safety process
Strategic Safety Planning
A strong safety program requires thorough planning and execution. We assist with the development of verification and validation plans, ensuring that safety measures are tested and documented. Our strategic safety planning services include:
- Verification plans to confirm compliance with safety standards
- Validation plans to ensure systems function as intended
- Validation testing assistance for thorough safety evaluation
Safety Lifecycle Support
Our expertise spans the entire safety lifecycle, from risk assessment to ongoing maintenance and compliance. We provide:- Risk Assessments – A process that begins with a risk analysis to identify hazards, followed by a hazard analysis to determine the severity of each hazard (from minor incidents like a papercut to serious injuries like losing a finger)
- Mitigation Planning – Develop targeted strategies to reduce both the likelihood and impact of risks
- Safety System Implementation – Design, install, commission, and verify custom safety solutions
- Ongoing Support – Provide continuous maintenance and updates for long-term compliance and safety
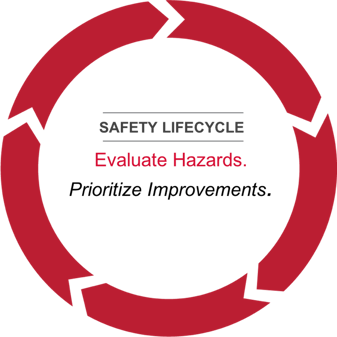
Plantwide Risk Assessments and Audits
Understanding and mitigating risk is essential for maintaining a safe plant environment. Our assessment and audit services help you stay ahead of compliance requirements and improve overall safety. These include:
- Team-based risk assessments/analysis
- Cybertrol will perform this as a facilitator with customer machine experts
- Typical people involved: operations, maintenance, engineering, environment, health, and safety, etc.
- Cybertrol will generate an executive report summarizing our findings from the risk assessment
- Hazard evaluation and mitigation planning
- Compliance evaluations to align with regulatory standards
- Site surveys and safety audits
- Employee training and education on safety best practices
RIA TR R15.306-2016 Task-based Risk Assessment Methodology
We follow the Task-based Risk Assessment Methodology outlined in RIA TR R15.306-2016 because it provides clear, practical examples and offers the highest level of granularity for effectively assessing risks in our processes.
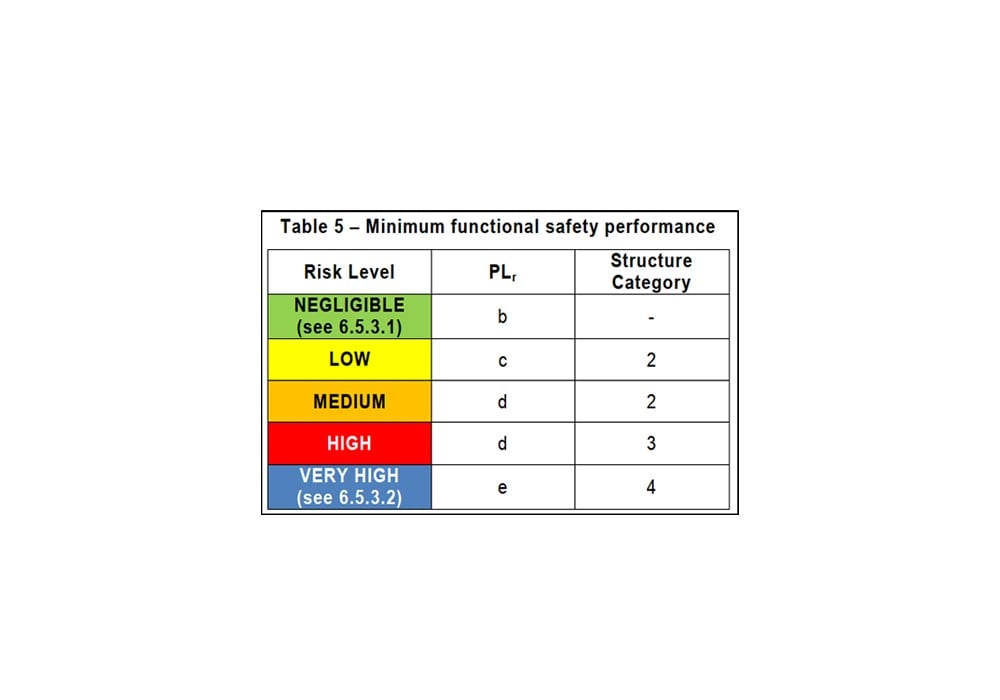
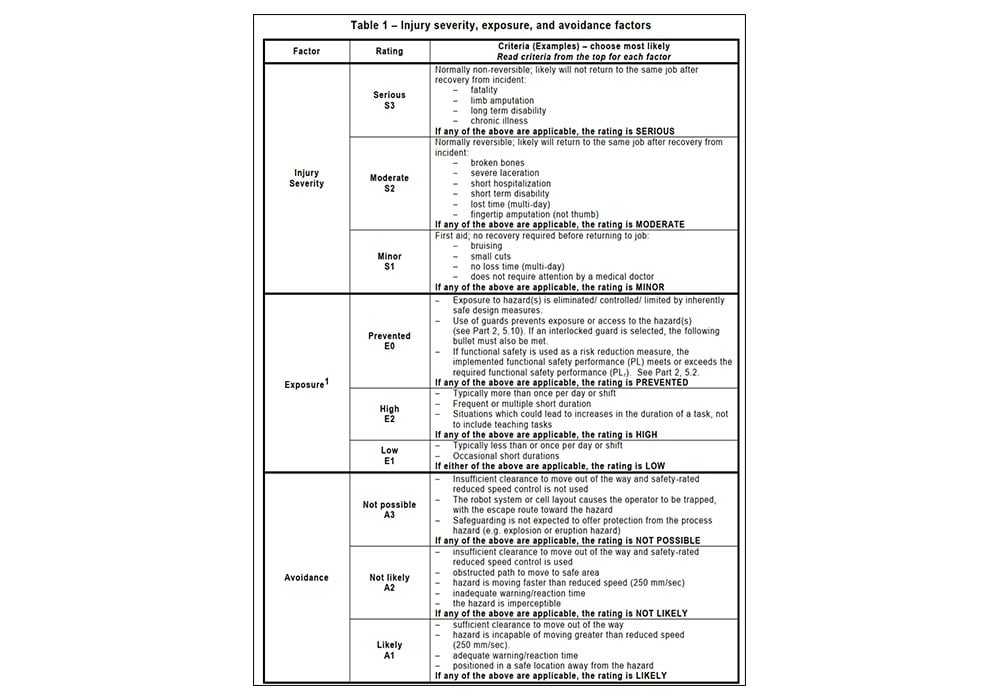
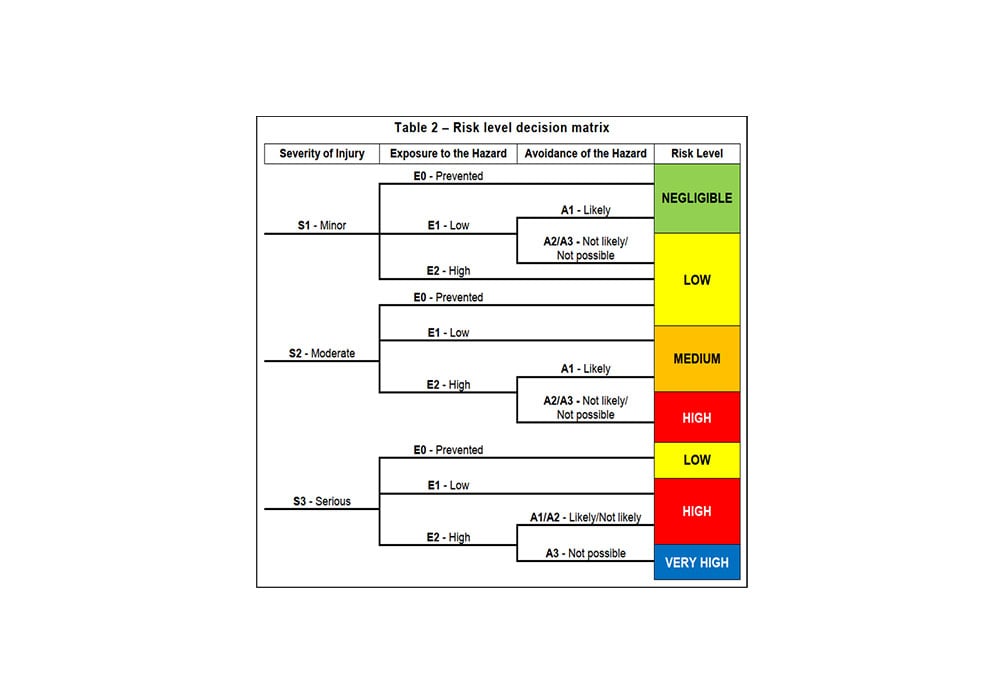
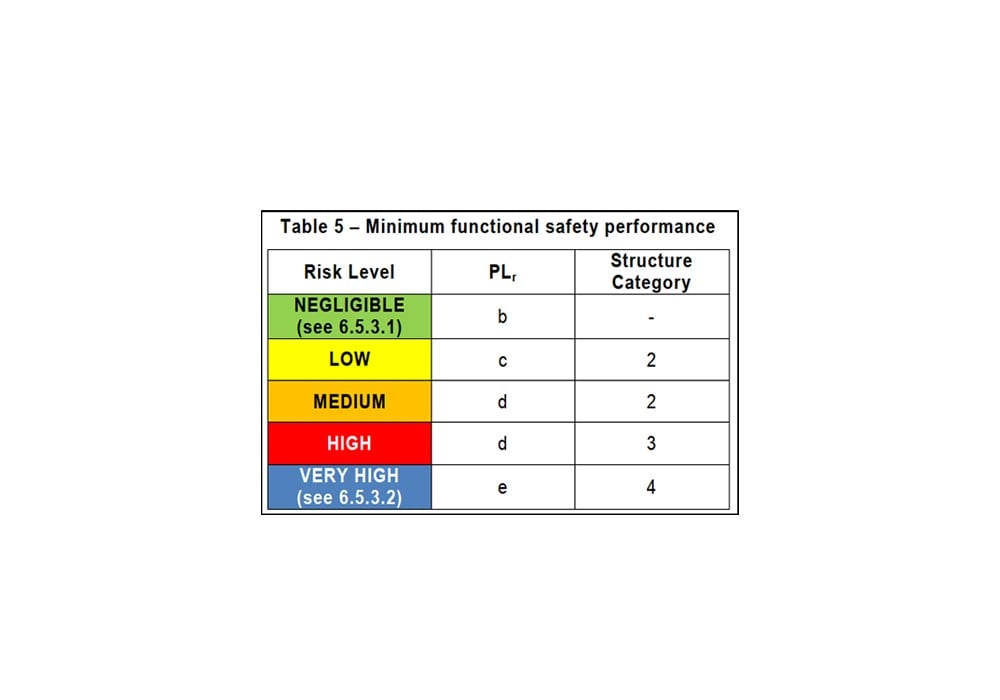
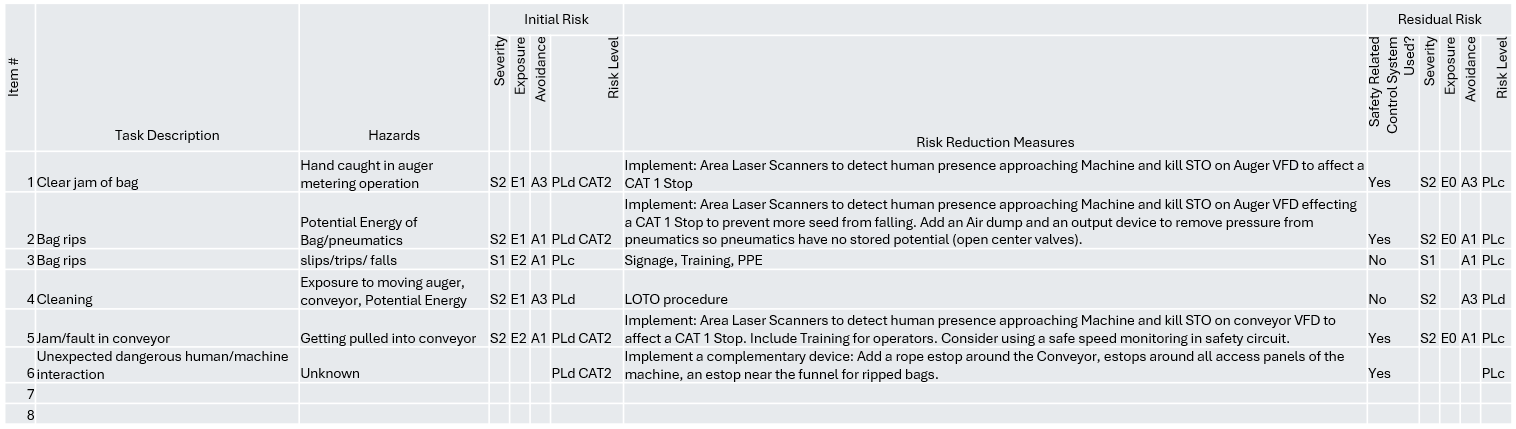
Sample Risk Assessment Using RIA TR R15.306-2016 Methodology - Cybertrol Engineering
Safety Systems and Compliance
We integrate functional safety into your existing control systems to improve compliance and enhance operational efficiency. Our safety system solutions cover:
- Hardware and software selection and design
- Safety programming and software development
- Integration with existing control systems
- Data collection and reporting tools for safety monitoring
Safety Systems Evaluation and Testing
Ensuring that your safety systems function as intended is critical. Our team provides thorough evaluations and testing services, including:
- SISTEMA reports for safety function analysis
- Reviews of circuit diagrams, programs, and calculations
- Functional testing to validate system performance
- Operational sequence testing to confirm proper machine behavior
- Factory and site acceptance testing (FAT/SAT)
- Fault injection and simulation to evaluate safety system response
Rockwell Automation Safety Capability and Partnership
- Conduct risk assessments and mitigation planning
- Develop safety requirement specifications (SRS)
- Perform circuit calculations and conformance analysis using SISTEMA
- Design, program, and implement safety system mitigations
- Develop and execute verification and validation protocols
Why Functional Safety Matters
Implementing functional safety measures can significantly reduce costs associated with workplace incidents. By leveraging automated sensors and programming, facilities can replace traditional Lockout/Tagout (LOTO) procedures and Pre-Job Hazard Assessments (PJHAs), streamlining maintenance while reducing administrative overhead. This approach enhances efficiency, minimizes downtime, and ensures safer, more effective operations. These improvements help mitigate costs related to workplace incidents, including:
- Lost production time due to accidents and unplanned downtime
- Costs associated with OSHA recordable incidents and compliance documentation
- Medical expenses, worker’s compensation claims, and lost labor hours
- OSHA fines, legal fees, and potential civil litigation
A strong commitment to safety helps maintain a positive reputation and promotes a safe work environment, which can:
- Improve employee retention and morale
- Attract skilled workers who prioritize safety
- Reduce the risk of brand damage due to safety violations
A well-implemented safety strategy enhances overall equipment effectiveness (OEE) and operational efficiency by:
- Reducing unplanned downtime due to safety incidents
- Improving worker ergonomics and system usability
- Preventing unauthorized machine access through safety interlocks and access controls
Contact us today to learn how we can help enhance the safety and efficiency of your operations.
Contact Us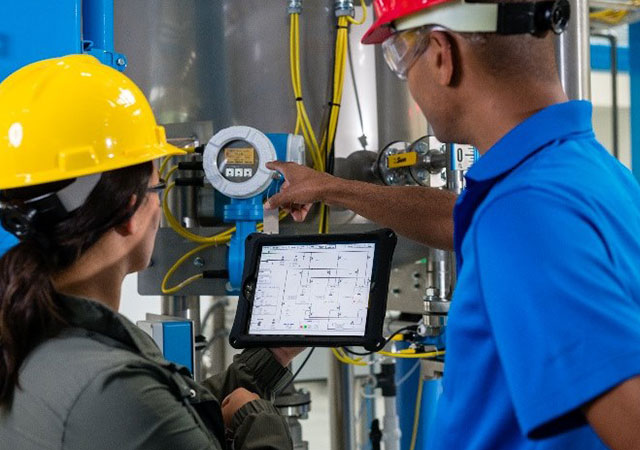