What is CIP?
Clean-in-place (CIP) is an automated method of cleaning the interior surfaces of processing equipment such as tanks, valves, pipes, and associated fittings without the need for major disassembly. CIP systems are widely used in industries that require high levels of hygiene such as food and beverage, dairy and cheese, and pharmaceutical.
The Downfalls of CIP with Fixed Cleaning Cycles
Traditional CIP systems have relied on fixed cleaning cycles and predefined parameters, which limits their ability to adapt to different equipment and process requirements. This lack of flexibility can lead to poor cleaning results, increased water and chemical usage, and longer than necessary cycle times. To further complicate the process, making changes to fixed CIP recipes, sequences, and procedures often requires issuing RFPs (requests for proposal), securing approvals, contacting sanitation or chemical experts, and waiting weeks for an engineering resource to make an on-site visit, just to make a straightforward change.
Cybertrol's CIP Solutions:
Empowering users with the most flexible CIP system controls
In response to the growing demand for more user-friendly CIP, Cybertrol has developed a configurable solution to provide the user with the most flexible CIP system control paired with comprehensive reporting capabilities. Our configurable CIP allows the user to build and edit recipes from the HMI (human machine interface) terminal. CIP circuits can also be managed from the HMI terminal with the ability to tailor circuit parameters and manage valve pulsing. Built-in system security ensures that only approved users can access the data for editing.
Features and Benefits
Cybertrol's user-configurable CIP systems offer a range of benefits that enhance efficiency and productivity, including:
- Optimal management of master recipes and circuit-specific routing and set points.
- On-screen modification of valve pulsing sequences.
- On-screen monitoring of permissives and interlocks.
- Robust reporting including sequence execution, analog trends, operator comments, titration verification, outlier detection, water and chemical usage.
- Can be applied to an existing system for a simple retrofit or a new installation.
- A template-based approach allows the system to be rapidly deployed.
- Ability to change valve pulsing sequence from the HMI.
Is your CIP working for you?
What CIP Parameters are Configurable?
Another feature of configurable CIP is the ability for the recipe creator/editor to make recipe steps that hold the system for an acknowledgement from the operator as well as provide a customized message for that acknowledgment. This gives the user the ability to request that the operator perform a certain action. The system will remain in the 'Hold For Acknowledge' step until the operator acknowledges the action.
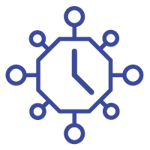
Tailored Cleaning Parameters
Our solutions allow operators to define and adjust cleaning parameters such as flow rates, temperatures, chemicals, and duration. Configurable parameters allow the user to optimize cleaning processes for different equipment or pipelines, ensuring thorough sanitation while minimizing resource consumption.
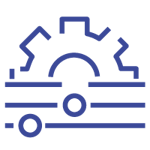
Process-Specific Programming
User-configurable CIP systems leverage advanced control system integration and automation expertise. This enables the development of systems that can be seamlessly integrated into existing control systems. Operators can program specific cleaning cycles that align with different processes and equipment, streamlining operations and reducing manual intervention.
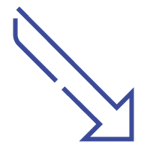
Reduced Resource Consumption
By allowing users to adjust cleaning parameters, configurable CIP systems minimize the use of water, cleaning agents, and energy. This reduction not only lowers operational costs but also contributes to sustainable practices by minimizing resource waste and environmental impact.
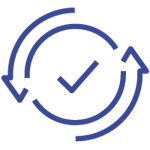
Faster Cleaning Cycle
Configurable CIP systems optimize cleaning algorithms and leverage automation, precise control, and real-time monitoring. These advancements result in faster cleaning cycles, reducing downtime, and maximizing operational efficiency. Users can quickly and effectively clean equipment, allowing for more production time and increased productivity.
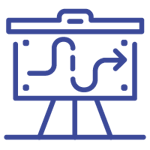
Enhanced Compliance and Traceability
User-configurable CIP systems facilitate compliance with industry regulations and standards. Our systems include data logging and tracking functionalities, providing comprehensive records of cleaning cycles. Plus, they also capture the operator that performed the wash and have the ability to collect required quality/HACCP parameters, such as chemical concentration titrations. This documentation enables auditing, regulatory compliance, and demonstrates adherence to sanitation standards.
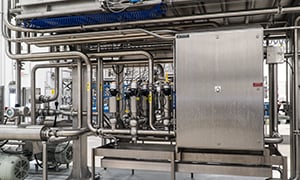
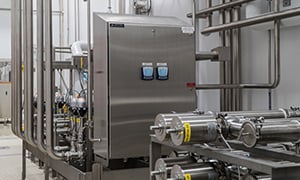
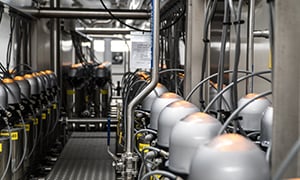
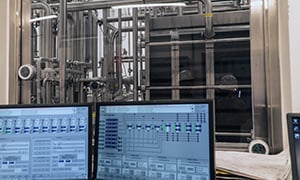
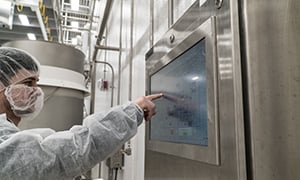
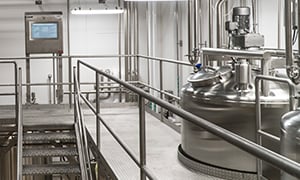
Cybertrol's Robust CIP Reporting Capabilities
CIP Completed Washes Report: A completed washes report shows the circuits that were washed on each CIP system (supply pump) can be used to either quickly validate that any/all required circuits were washed as well as provide efficient access to individual wash reports.
CIP Wash Report: The CIP wash report consists of historian trends showing flow, temperature, and conductivity, as well as event-based reports that list the steps taken, the duration of each step, and exceptions during operation. Exceptions will include holds for temperature, flow, or conductivity, operator actions such as “advance step” or other failures during a circuit. The operator will be prompted for digital entry of initials for validation purposes and a confirmation step will be required—before the CIP completes—to ensure that all data has been collected.
CIP Outlier Report: The CIP outlier report is used to quickly identify washes that have occurred that contained exceptions. Exceptions may include excessive water or chemical usage, unusually long duration, or operator activity such as logged comments or operator-aborted wash cycles. Having this information readily available allows for more efficient review of historical washes as it draws attention to questionable wash cycles rather than manually reviewing each wash report.
CIP Chemical Usage Report: The CIP chemical usage report allows sanitarians and/or chemical providers to review chemical usage on a per-wash, circuit, or CIP system basis. This information is helpful for validating the amount of chemical used for each circuit is appropriate and helps identify areas of opportunity to minimize chemical usage.
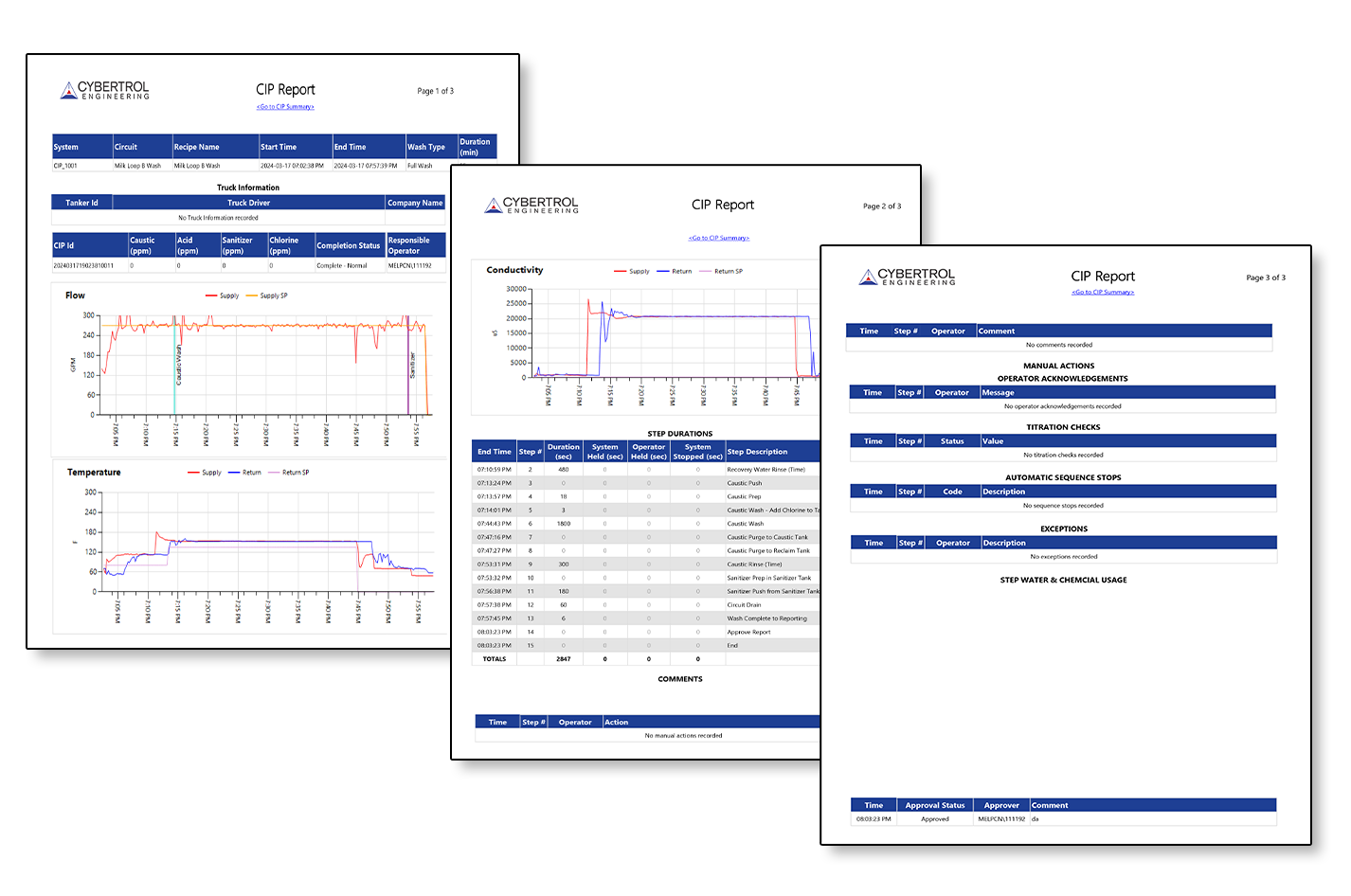

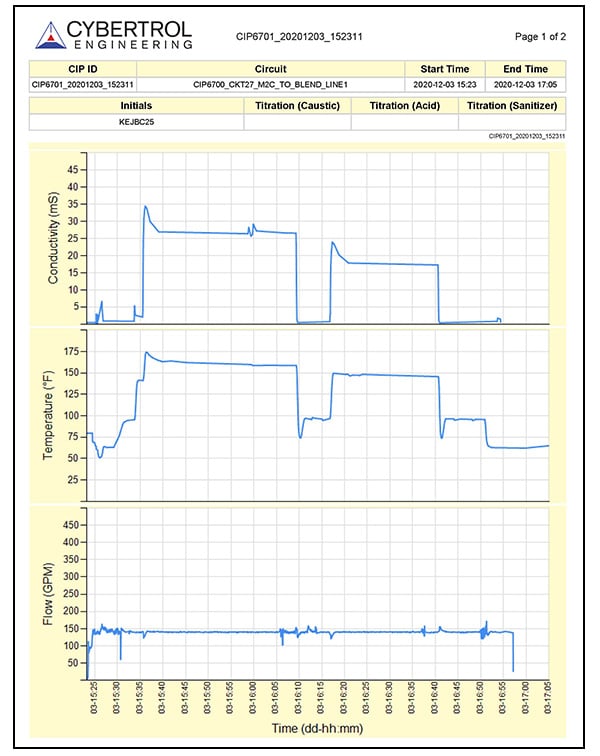
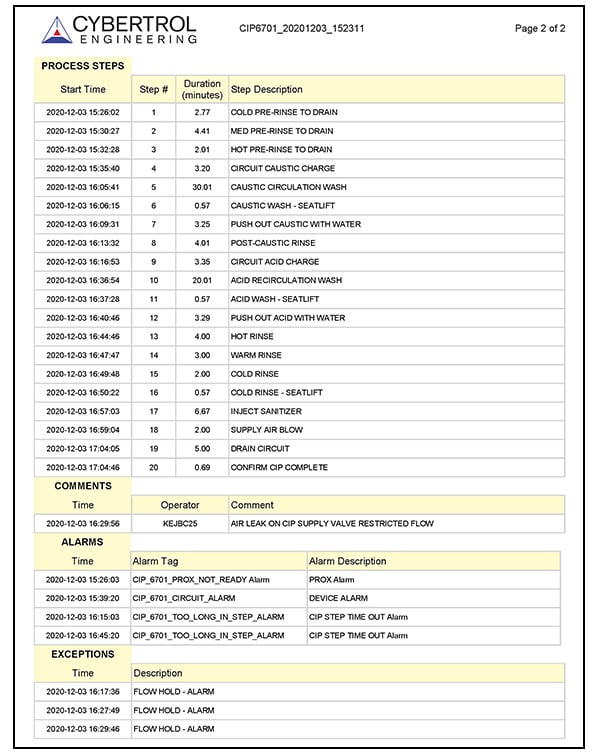
Contact Cybertrol for a user-configurable CIP solution that ensures effective and efficient cleaning practices.
Contact Us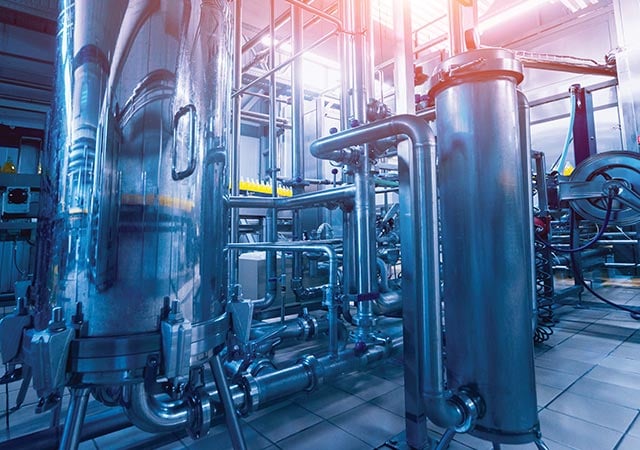